MADE IN SHEFFIELD: Summitglow puts the heat into industry
and live on Freeview channel 276
And today – from the same site in Sheffield – hundreds of big name companies rely on Summitglow’s heat treatment services to keep them in business.
For the firm is an expert at making steel components tougher and harder – much harder.
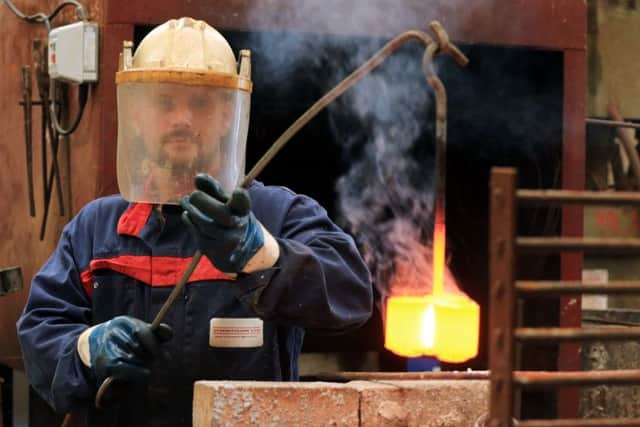
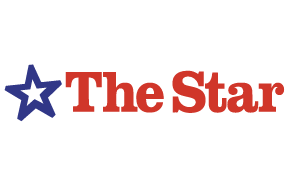
Advertisement
Hide AdAdvertisement
Hide AdBoss Philip Watkinson explains why it is a vital step in the manufacturing process: without it a masonry bit is softer than the brick it is supposed to drill holes in. And that toughening process is required by thousands of steel products, from surgical instruments to scissors.
The company, which has sites on Watson Street, where Firth Brown once operated, and Harleston Street in Attercliffe, has 250 customers. A quarter are in Sheffield, including Technicut, Gripple, scissor maker Ernest Wright and medical instruments firm Platts and Nisbett.
But it’s not just a case of bunging stuff in the oven – one blunder and a part that has been intricately machined for hours can end up as scrap.
It’s not alchemy but it’s not far off.
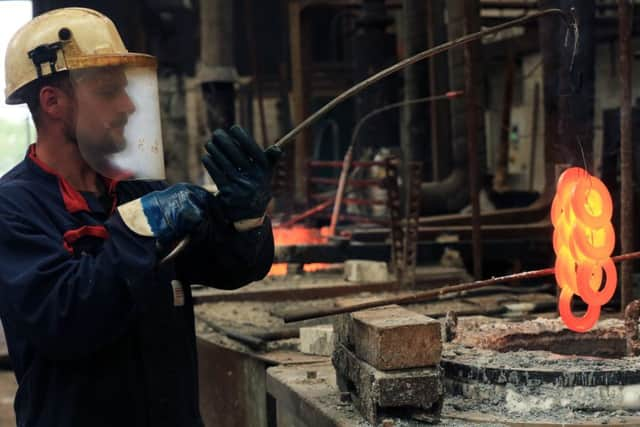
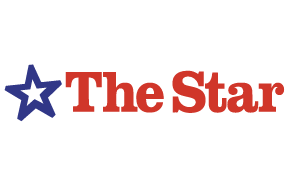
Philip said: “The reality is if heat treatment isn’t done correctly the product is useless.
Advertisement
Hide AdAdvertisement
Hide Ad“Customers trust us with their parts and they want them back in the correct state. And they want it turning around quickly because they have got a product to sell. Years ago people used to have stock, now everyone’s hand to mouth.”
Fundamentally, the process involves heating, followed by fast cooling for hardness, then heating and slower cooling for toughness.
Summitglow has kept pace with industry which today uses thousands of formulations of steel, each one requiring a different approach to get the best from the metal.
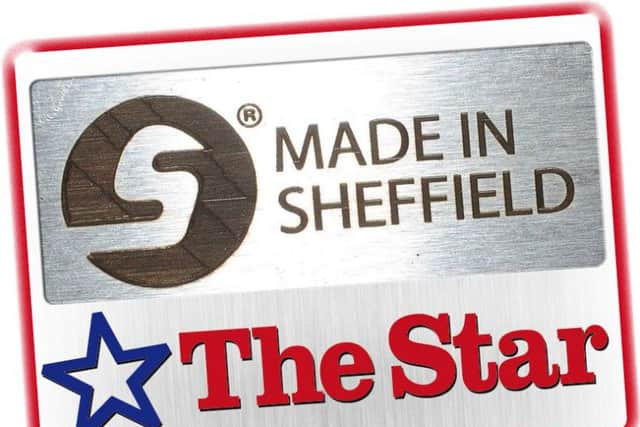
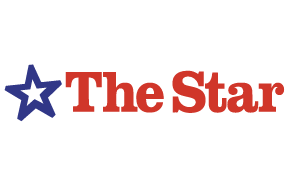
The firm boasts 28 furnaces and a range of treatments from a 1,300 degree molten salt bath to a vacuum furnace.
Advertisement
Hide AdAdvertisement
Hide AdIt is one of just two such companies left in the city following the decline of industry. But it is on course to have its best year ever.
Its manufacturing customers are booming – the heat treatment industry is known as a barometer of business – and it has an incredible depth of knowledge.
Works manager Greg Atter, who has worked at Summitglow for 33 years, says companies will often call for advice when they are planning a new product.
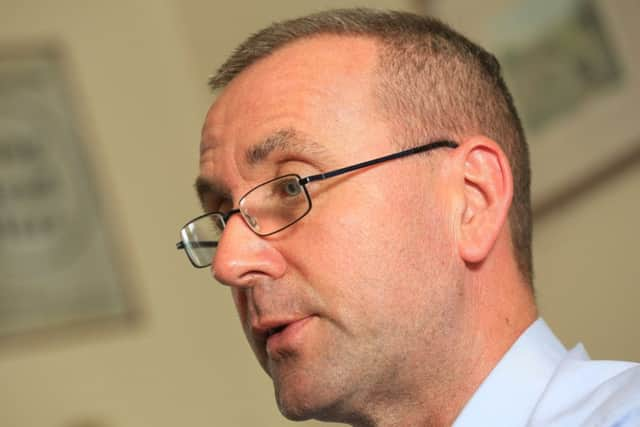
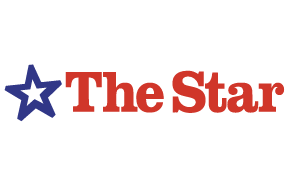
Summitglow also saves its customers money. In the old days many steelworks would have their own heat treatment departments.
Advertisement
Hide AdAdvertisement
Hide AdBut gradually it became cheaper to outsource it, despite items having to be ferried across the city in a process that can take a full day.
Furnaces need to be busy 365 days-a-year to pay their way. The firm’s power bill is £24,000 a month.
Summitglow was set up in 1983 when Qualcast closed and Philip’s dad was made redundant. With two pals he bought its assets and set up in business.
Today the firm operates on two sites and employs 25.
At Harleston Street, Nigel Rider is treating machine knife blades using three baths of molten barium chloride at 850, 1,150 and 560 degrees.
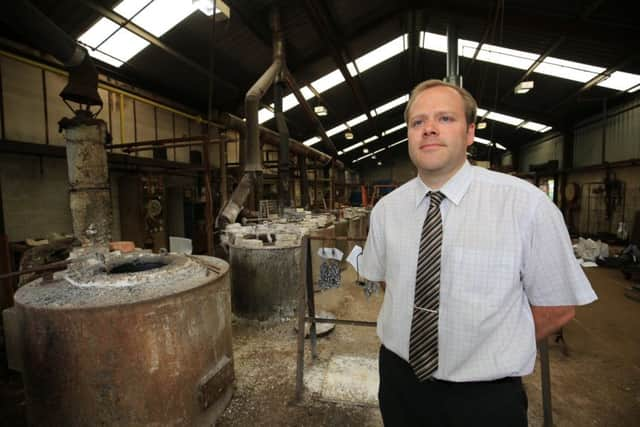
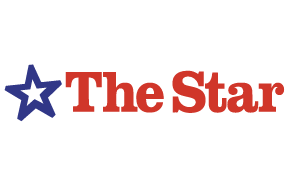
Advertisement
Hide AdAdvertisement
Hide AdHe lowers them into the first for a pre-set time, then transfers the basket into the hottest for five minutes before they are moved, glowing red hot, to the final bath.
Finally, they are placed on a tray to cool.
The other site has computer-controlled vacuum furnaces.