£8m investment in rescued Rotherham metal firm
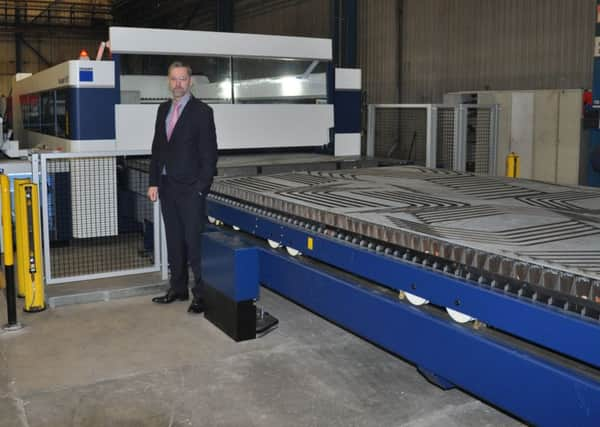
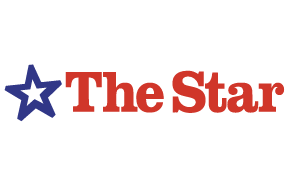
MTL Advanced says the giant TruLaser 8,000 is faster, more accurate and uses 40 per cent less energy than the machine it replaced. It is part of a modernisation drive to boost productivity.
Karl Stewart, commercial director said: “Our investment will enable us to remain at the forefront of our industry, as there are very few companies in the UK with this level of technology in-house.
Advertisement
Hide AdAdvertisement
Hide Ad“Investment in large format cutting machines has been at the core of MTL’s past successes.”
MTL Group collapsed into administration in February, with the loss of 157 jobs, following the loss of an overseas defence contract.
Some 135 jobs were saved after WEC Group, of Darwen, Lancashire, bought the business.
Now, it is buying MTL’s factory and six acres of land on Grange Lane for £7m, to give the company room for expansion.
Advertisement
Hide AdAdvertisement
Hide AdMr Stewart said since the acquisition, 45 jobs had been created and a recruitment drive was underway. MTL had achieved month-on-month profitability and built up a strong order book for 2016 thanks to several new multi-million pound contracts, he added.
WEC is one of the largest engineering and fabrication companies in the UK. Last year it invested £2.5m in equipment at its Blackburn sites and in the new Darwen-based powder coating division, launched in 2014.
WEC Group commercial director, Wayne Wild said: “Lean manufacturing techniques and automation are essential to our growth and continuous improvement strategy. We have made several other similar investments in a 640 ton, fully-automated robotic press brake as well as 13 robotic welders. It is a step forward in the automation of our manufacturing process.
“We can now profile, press, and weld components of up to 6m in length with minimal involvement from operators, so we can guarantee the highest quality.”