How a historic craft has made a Sheffield dad and daughter the business
and live on Freeview channel 276
The silversmiths are father and daughter Brett and Kat Payne, based in Persistence Works in Brown Street in the city centre.
The business is called Brett Payne and as the bang of the drop hammer hits, it crispens up the silver and means the material can be made into spoons. The tool is more than 100 years old.
Advertisement
Hide AdAdvertisement
Hide AdThe crash and wallop happens on another part of Sheffield history - three genuine Mousehole Anvils. By the end of the 18th century Mousehole Forge, situated in the Rivelin Valley, was one of the leading exporters of anvils to America, where they are now highly sought-after collector’s items.
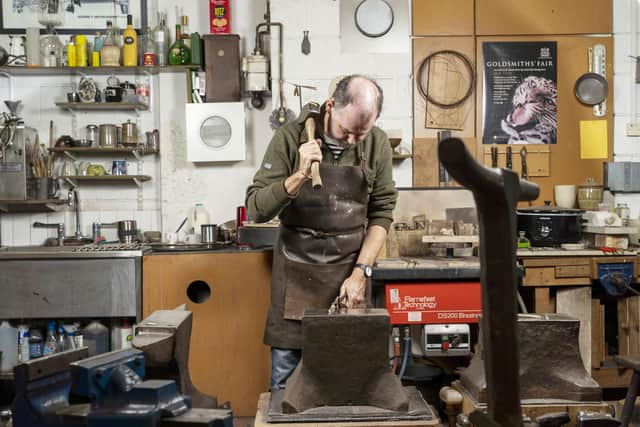
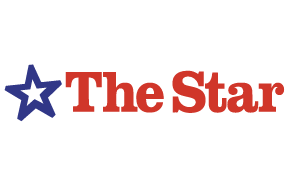
The anvils in the Payne workshop have the forge’s distinctive corporate mark – a mouse followed by the word ‘hole’.
They are arranged in the middle of the workshop floor and are at the heart of everything the Paynes do.
Brett says: “It’s an ancient craft. Low technology requires a high degree of skill. Silver is mostly worked cold but there’s a tradition kept alive in Sheffield where it is forged hot.
Advertisement
Hide AdAdvertisement
Hide Ad“It was kept alive because of cutlery. I came across the process in a workshop on Arundel Street and thought it was magic.
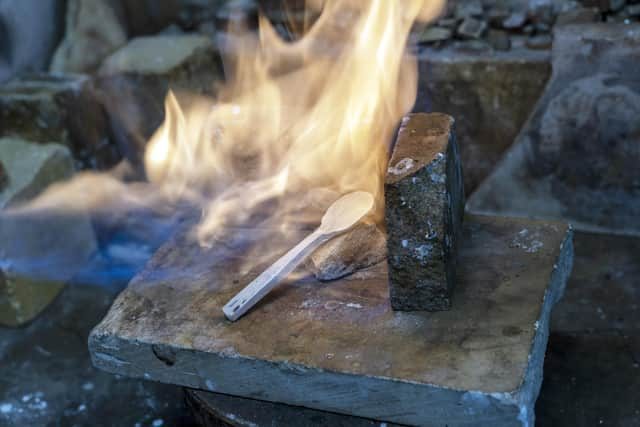
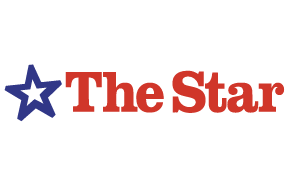
“I developed it to make other objects like candlesticks.”
This is how he combines the old and the new. “There are strengths and weaknesses for both. There is world class experience of working silver in Sheffield, it is unique but often the traditional skills and design is so dominant it is difficult to introduce new design.
“The design ethic in Sheffield was a throwback to Victorian times, not contemporary. The modern home meant the times of a dining table were becoming less relevant.”
Kat adds: “The anvils are older than me and dad put together as is the drop hammer. Hot forging is one of the oldest techniques in the world. It hasn’t changed in thousands of years because there was no need for it to.
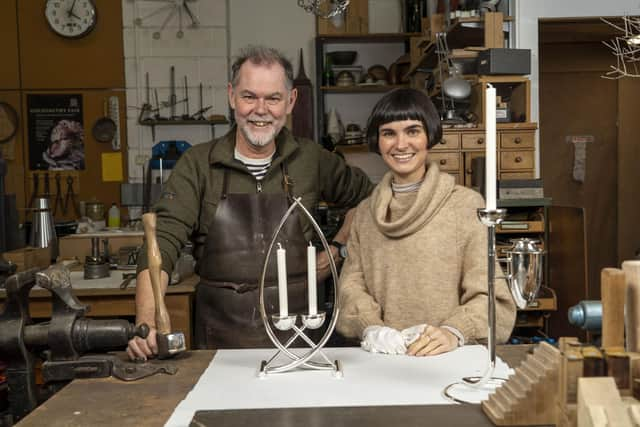
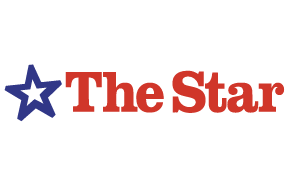
Advertisement
Hide AdAdvertisement
Hide AdThey have a polishing booth sectioned off in the workshop. “It’s enclosed because it produces a compound which makes everything dirty.
“We set aside a day for that and don’t come home on the bus because you look like a chimney sweep.”
Kat and Brett, aged 62, live in Millhouses. Brett set up his business in 1983.
He was born in Kent but came to Sheffield in 1978 to study at Psalter Lane art college. He wanted to set up as a silversmith and with a group of artists and craftspeople found an old cutlery factory in Matilda Street in the city centre.
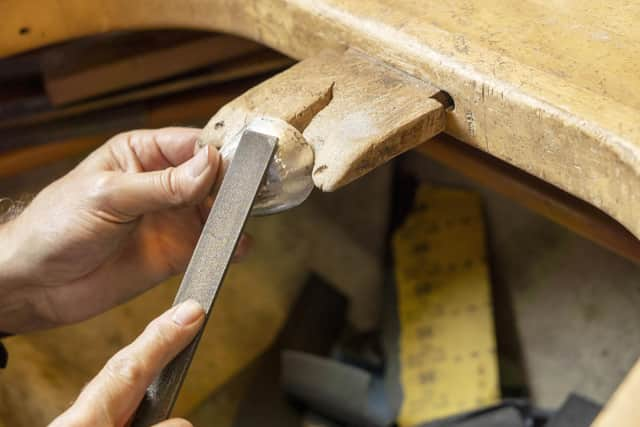
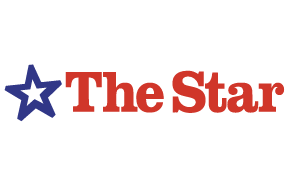
Advertisement
Hide AdAdvertisement
Hide AdThey revamped the place as Sydney Works, which is now the University Technical College.
“I came here because I wanted to be a silversmith and they did a silversmith degree at Psalter Lane. I had seen Made In Sheffield on tools and cutlery so when I decided to be a silversmith I was told I had to go to Sheffield.
“There is no better place in the world to do it.
“We sell work all over the world and everywhere we go people associate Sheffield and silversmiths.”
Kat, 32, went to school at Nether Green Infants and then Sheffield Girls High. She read modern and medieval languages at Cambridge.
Advertisement
Hide AdAdvertisement
Hide Ad“I grew up with this trade and I can remember coming in here and doing piecework to earn pocket money. I’ve been in and out of workshops for as long as I can remember. It has been the backdrop of my life.
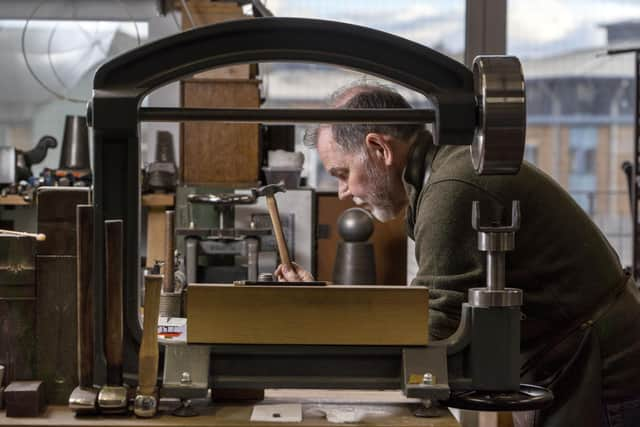
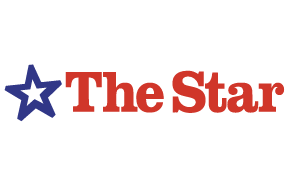
“I chose languages because I wanted to travel but it came in useful for dad.”
Brett was negotiating with a European firm over a design but the exchange of emails in German were taking weeks to translate, delaying the deal.
“I used my German skills to negotiate a contract and suddenly everyone understood each other and in the process I helped dad,” says Kat.
Advertisement
Hide AdAdvertisement
Hide AdShe joined Brett for a Goldsmiths Fair in London, where artists from around the world display their wares. “It was one of the most exciting jobs I had ever done.”
So with no formal training or qualifications, Kat has learned everything in Brett’s workshop.
She is in good hands. Brett is a Liveryman of the Worshipful Company of Goldsmiths, a Freeman of the Company of Cutlers in Hallamshire and a past chairman of the Goldsmiths Craft and Design Council.
Oh yes, he’s exhibited in the Pompidou Centre, Paris, the Museum of Modern Art in Kyoto, Washington, New York, Seoul and Berlin.
Advertisement
Hide AdAdvertisement
Hide AdSo how do they get along? Kat grins and says: “It’s a dream, there’s never a cross word!”
Brett adds: “It works quite well. We complement each other. I do most of the silversmithing, there’s not too much conflict.
Kat agrees. “I’ve got a good understanding of what dad does, I can forge, use the polishing mop, but dad is the expert and master craftsman.
“Family working together can either be a dream or a nightmare and for me it works like a dream.”
Advertisement
Hide AdAdvertisement
Hide AdAnd there is no suggestion she is woman in a man’s world. “Traditionally this would have been a man’s world,” Kat acknowledges.
“Historically there were women in the silver industry like the buffer girls, a skilled job, but an allied trade - most forgers, and little mesters were male.
“That’s not the case now. The world of silversmithing and jewellery making is predominantly female. That’s come into effect in the last 40 years.”
As if to prove the point, fellow silversmith Helena Russell is in the workshop, where she does a day a week for Brett.
Advertisement
Hide AdAdvertisement
Hide AdKat says: “If you were a young man coming into the industry now you would be in the minority.”
Now Kat and Brett have a vision for the Goldsmiths Fair which gave her the silversmith bug. It is about to celebrate its 40th anniversary in London, the longest running event of its kind.
Kat says: “We decided it needed a partner event outside London and as we are based in Sheffield we set up a connected but independent enterprise called Goldsmiths North.”
It is sanctioned and supported by the Goldsmiths Company Charity, the Sheffield Assay Office and the Cutlers Company in Hallamshire. The first Sheffield event was in 2019 at the Cutlers Hall.
Advertisement
Hide AdAdvertisement
Hide AdBrett says: “You can sit around in a pub talking about doing it until the cows come home. We thought, let’s do it.”
So they did and 3,000 people visited in three days. “We were delighted,” says Brett.
Then came lockdown. Plans for a 2020 event had to be postponed and after spending a couple of months at home, they ventured back to the workshop, mindful of covid restrictions.
Inevitably, there were no exhibitions to go to so from March 2020 to August 21 they had an imbalance where they could make, but not sell.
Advertisement
Hide AdAdvertisement
Hide AdKat says: “We made spoons for a year. Spoons are a good go-to exercise if you’re a silversmith. It’s a technical task.
“A lot of what we do is hot forged, hammered out from a bar, it is all about getting the shape you want.
“The purest expression of that is a spoon because you are really only using one technique, our signature technique, the way spoons were made in an era before the industrial revolution. It is history in action.”
Now they are looking forward to the future. Goldsmiths North will be back next year at the Cutlers Hall from July 8 to 10.
Advertisement
Hide AdAdvertisement
Hide AdBrett says: “We envisage an annual event at the Cutlers Hall which is a celebration of the highest quality of silverware and jewellery in Sheffield for the reasons of tradition, heritage and the Assay Office.
“We want to attract international makers and they want to come to Sheffield because it is a centre of excellence. We want Sheffield to be the place where the best exhibit.
“That will bring people to the city who will spend money here and reaffirm Sheffield’s name as a centre.”
As you can tell, he’s proud of the city. “I’ve been here longer than anywhere else. I am a Sheffielder!”
Advertisement
Hide AdAdvertisement
Hide AdBrett’s work has included a light ball centrepiece for the House of Lords in 2012. He is cagey about the price but agrees it was more than £30,000.
At the other end of the spectrum, you can buy a cocktail stick for £150.
Kat likes the business because it connects her with people. “You get a brief window into people’s lives, when they are celebrating good times - a wedding, anniversary or birthday.
“They want to mark a family occasion and that is extremely gratifying because we tend to meet everyone we make for. It starts with a bullion delivery and ends with placing a candle on their table.”
Advertisement
Hide AdAdvertisement
Hide AdThe Paynes are part of the Open Studios event hosted by Yorkshire Artspace on November 20-21. More than 160 artists will take part at Persistence Works and Exchange Place Studios, on Exchange Street.
Visit www.artspace.org.uk for details. To view Brett and Kat’s work visit https://brettpayne.com/